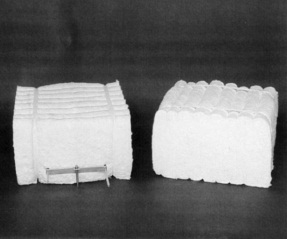
Price: on request
Z-Blok 3 refractory modular blocks are convoluted blanket modules which combine the excellent thermal characteristics and proven service performance of Thermal Ceramics’ Z-Bloks with the ease of installation and versatility of the T-Bar anchoring system. They are made from high quality spun-fibre Blanket, folded and pre-compressed to a specified density, and held in position with 2 stainless steel tubes, mounted transversely within the module. The modules can be supplied encapsulated in plastic film, which ensures dust levels are kept to a minimum during installation. During installation, the modules are further compressed, the resilience of the fibre and recovery after the restraining bands are removed ensuring tightly-compressed intermodular joints.
Type:
convoluted blanket anchored modules.
Maximum continuous use temperature:
Kaowool S/Маты Cerablanket - 1260 0C
Kaowool SZr/ Маты Cerachem - 1425 0C
Маты Cerachrome - 1425 0C
The maximum continuous use temperature depends on the application. In case of doubt, refer to your local Morgan Thermal Ceramics distributor for advice.
Features:
The Z-Blok 3 module offers several advantages to both the furnace constructor and the end-user.
• the Z-Blok 3 module maintains the light weight, thermal efficiency and resistance to thermal shock characteristics of ceramic fibre linings;
• the decompression of the blanket folds gives tightly sealed inter-modular joints;
• the resilience of the blanket can accommodate some flexure of the furnace casing without opening gaps between modules;
• the unique T-Bar fixing system is exceptionally simpleand quick to install;
• the resilient blanket is resistant to mechanical damage;
• where damage occurs, individual modules can be easily replaced;
• it is versatile and the modules can easily be cut, on site to suit awkward configurations;
• the anchor system is buried inside the module and close to the casing. The metal components are therefore maintain at low temperature;
• the ASTM 316 stainless steel has a high corrosion resistance and maintains its creep strength to a relatively high temperature;
• the system ensures that the fibre is pulled back into intimate contact with the furnace casing or any substrate with no bridging of irregularities, thus eliminating convective heat transfer behind the lining;
• the system readily adapts to include vapour barriers and backing blankets.
Applications:
Z-Blok 3 has a multitude of uses in heat containment applications in all industry groups, a selection of which are as follows:
• Petrochemical (process heaters, reformers, ductwork and pyrolysis heaters);
• Iron and Steel (transfer ladle lids, soaking pit covers, reheating furnace, multi and single stack coil annealing furnaces, continuous annealing and coating furnaces, rotary hearth furnaces, car bottom furnaces, roller furnaces, lift-off furnaces, offtakes and ductwork);
• Aluminium (soaking pits and covers, bale out furnaces, homogenising furnaces and ductwork);
• Ceramic (tunnel kilns for whiteware and red brick, intermittent kilns for whiteware and red brick, Hoffman Kilns and ductwork);
• Utilities (thermal oxidisers, waste heat recovery units, combustion chambers and boiler ductwork).
Fixing components:
The studs and nuts are M6 threaded in ASTM 316 stainless steel, unless otherwise specified by the customer. The standard T-Bar yokes are in ASTM 316 stainless steel, but higher grades of steel (ASTM 310 or Inconel 601) are available for more arduous service conditions.
Dimensions & Availability:
• The modules as normally supplied are 305mm square and thickness ranging from 100mm to 350mm in 25mm steps, though other sizes and densities are available on request.
• T-Bar yokes, studs and nuts are supplied as separate items, to be included in an order. It is recommended that the order includes sufficient spare studs to cater for setting-up the welding conditions and allow for any mis-fires.
Packaging:
Z-Blok 3 are packed in cartons or on pallets which are shrink wrapped.
Installation:
Full details of the recommended technique for installing Morgan Thermal Ceramics modules are included in our Module Installation Manual.
Сlick at the picture to view full size